Microwire Brush Electrodes - nimh-nif/SCNI_Toolbar GitHub Wiki
- Electrode Development
- Ide-McMahon Microdrive (2014)
- Microdrive cap with embedded connectors (2017)
- Chamber base with detachable connector casing (2018)
- Multi-nanodrives
- References
The microwire 'brush' array electrodes that are now commonly used in the SCNI were initially developed in collaboration with Igor Bondar and first reported by Bondar et al., 2009. The concept is to take a bundle of insulated microwires and insert them into the brain through a guide tube. As the electrode tip is lowered, the individual wires splay out in the tissue, allowing for stable isolation of extracellular spiking activity for a local population of neurons over long time periods. Each microwire consists of a nickel-chromium-aluminum core of 12.5 µm diameter, insulated with polyimide by the manufacturer (‘IsaOhm’, Isabellenhuete, Germany). These electrodes are currently commercially available from MicroProbes, MD in lengths from 2.5 mm to 120 mm.
While this basic electrode design continues to be used in the SCNI, we are continuing to develop the implant hardware that houses the electrode, mircrodrive, and connectors. A chronically implantable microdrive designed by David Ide and David McMahon at the NIH was first published by McMahon et al., 2014 and is currently available commercially from Hybex.
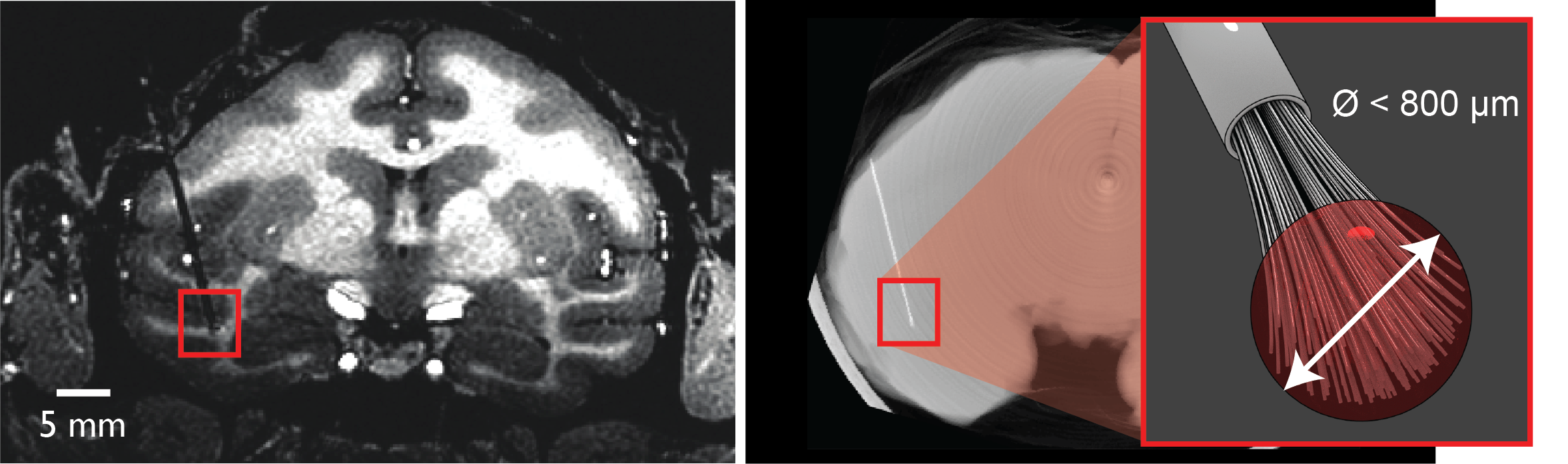
In order to improve our cell yield per implant, we attempted moving from 64-channel bundles to 128-channel bundles several years ago. However, our experience was that 128-channel bundles do not produce comparable yield to 64-channel bundles, possibly due to the mechanical properties of the increased bundle size. We subsequently reverted to using 64-channel bundles, but also miniaturized the microdrive design in order to obtain between 128-256 channels per implant using multiple 64-channel bundles.
During our tests to discern why the 128-channel bundles might not be working as well as we had hoped, Dr Kenji Koyano performed a series of tests, producing microwire bundles with a variety of tip designs, and inserting them into gelatin as a simulated brain tissue medium. His observations of how the individual microwires deflect upon entering the gelatin are show below (Figure 3). The results suggest that a non-flat tip shape and active pre-splaying of the wires prior to insertion in the guide tube both improve splaying of the wires in tissue.
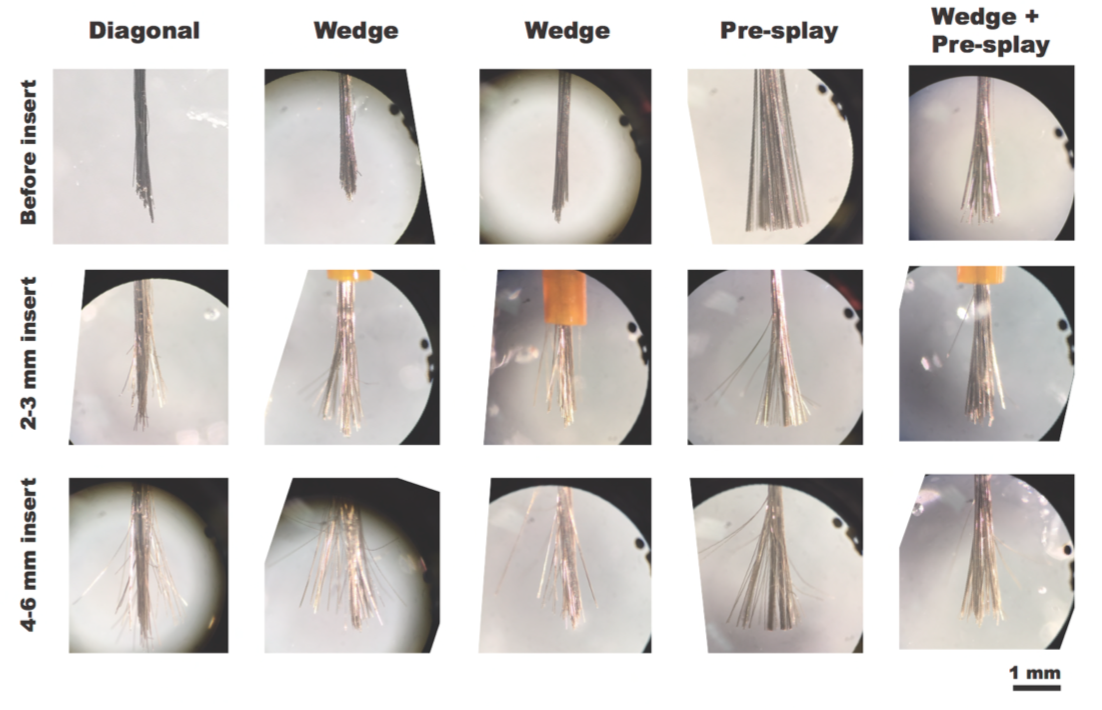
This original design for a chronically implantable microdrive was conceived by David Ide (SI) and David McMahon (SCNI), and was published in McMahon et al., 2014. The drive itself consists of three Ultem disks, stacked on three ceramic rods, with a single central PEEK drive screw. Turning the screw (accessible from the top of the drive) advances or retracts the central drive disk, to which the electrode shaft is clamped. The drive mounts to a cylindrical (19mm diameter) Ultem chamber base via two nylon screws, and is protected by an Ultem cap, which attaches via four brass set screws.
- When placing your microwire brush array order with MicroProbes, specify that the epoxy on the back of the Omnetics connectors must not exceed the width of the connector itself in order to be able to space adjacent connectors correctly.
- Arrange to send MicroProbes the 3D-printed connector casing in advance, so that they can epoxy the Omnetics connectors directly into the casing with the correct spacing.
- Bondar IV, Leopold DA, Richmond BJ, Victor JD, Logothetis NK (2009). Long-Term Stability of Visual Pattern Selective Responses of Monkey Temporal Lobe Neurons.
- McaMahon DBT, Afuwape OAT, Ide DC, Leopold DA (2014). One month in the life of a neuron: longitudinal single-unit electrophysiology in the monkey visual system.
- Mulliken GH, Bichot NP, Ghadooshahy A, Sharmab J, Kornblith S, Philcock M, Desimone R (2015). Custom-fit radiolucent cranial implants for neurophysiological recording and stimulation.
- Englitz B, David S, Depireux DA, Shamma SA (2011). The Array Drive : Optimizing the Yield and Flexibility of Chronic, Multielectrode Array Recordings
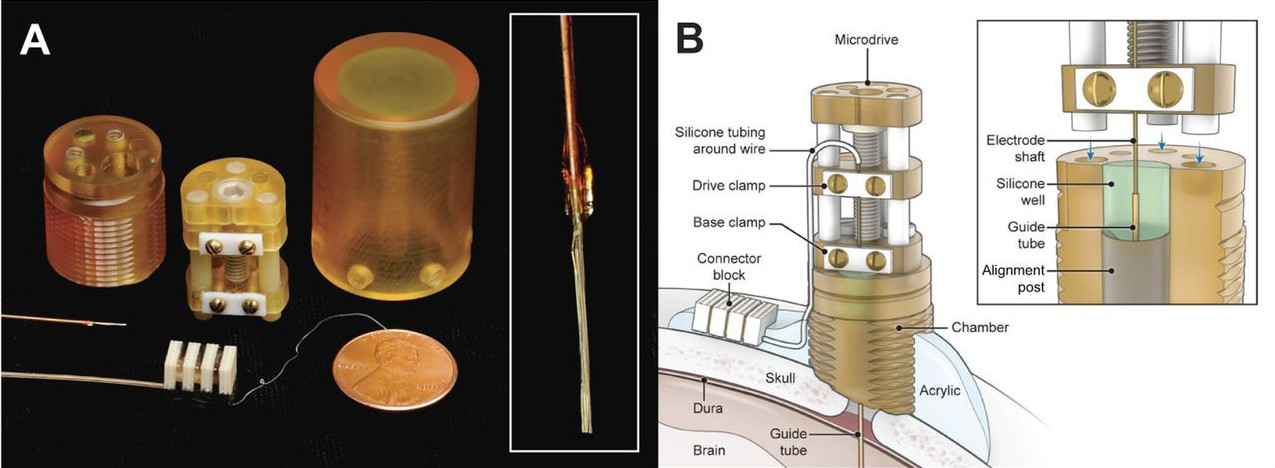
The original design was CNC machined from Ultem rods by the Section on Instrumentation at NIH. Since the design was published, it is now also manufactured by Hybex Innovations (Canada) with improved materials and minor modifications, and retails for $742.00 each. As a lower cost alternative, we also provide .stl files for 3D-printing this version of the microdrive here, and a list of additional parts needed for assembly below:
Supplier | Part # | Description | Quantity | Cost |
---|---|---|---|---|
Misumi | CSHLWH-PEEK-M4-16 | M4, 15mm PEEK socket cap hex screw | 1 | $2.30 |
McMaster | 27175A512 | M4 x 0.7 mm through-hole tap | 1 | $15.71 |
McMaster | 27175A112 | 4-40 through hole tap | 1 | $13.49 |
Grainger | 53MM63 | 0-80 thread tap | 1 | $20.30 |
McMaster | 87065K42 | 1/8" alumina ceramic rod, 12" | 1 | $20.94 |
McMaster | 92482A264 | 0-80 thread, 5/32" brass round-head slotted screws | 4 | $8.57 per 25 |
McMaster | 92942A718 | 4-40 thread, 5/16" Nylon Pan Head Slotted Screws | 2 | $6.04 for 100 |
McMaster | 92991A105 | 4-40 thread, 3/16" Brass Cup-Point Set Screws | 4 | $6.63 for 50 |
This cap is intended to protect the original cylindrical version of a chronically implanted microdrive, as described above. It additionally houses four 32-channel (36-pin) Omnetics connectors, allowing for up to 128-channel electrodes. It is intended for use with microwire brush arrays, as described by McMahon et al (2014) and currently sold by MicroProbes, and any low-profile headstage that uses Omnetics 32-channel nano connectors (including Intan RHD2164 64-channel boards).
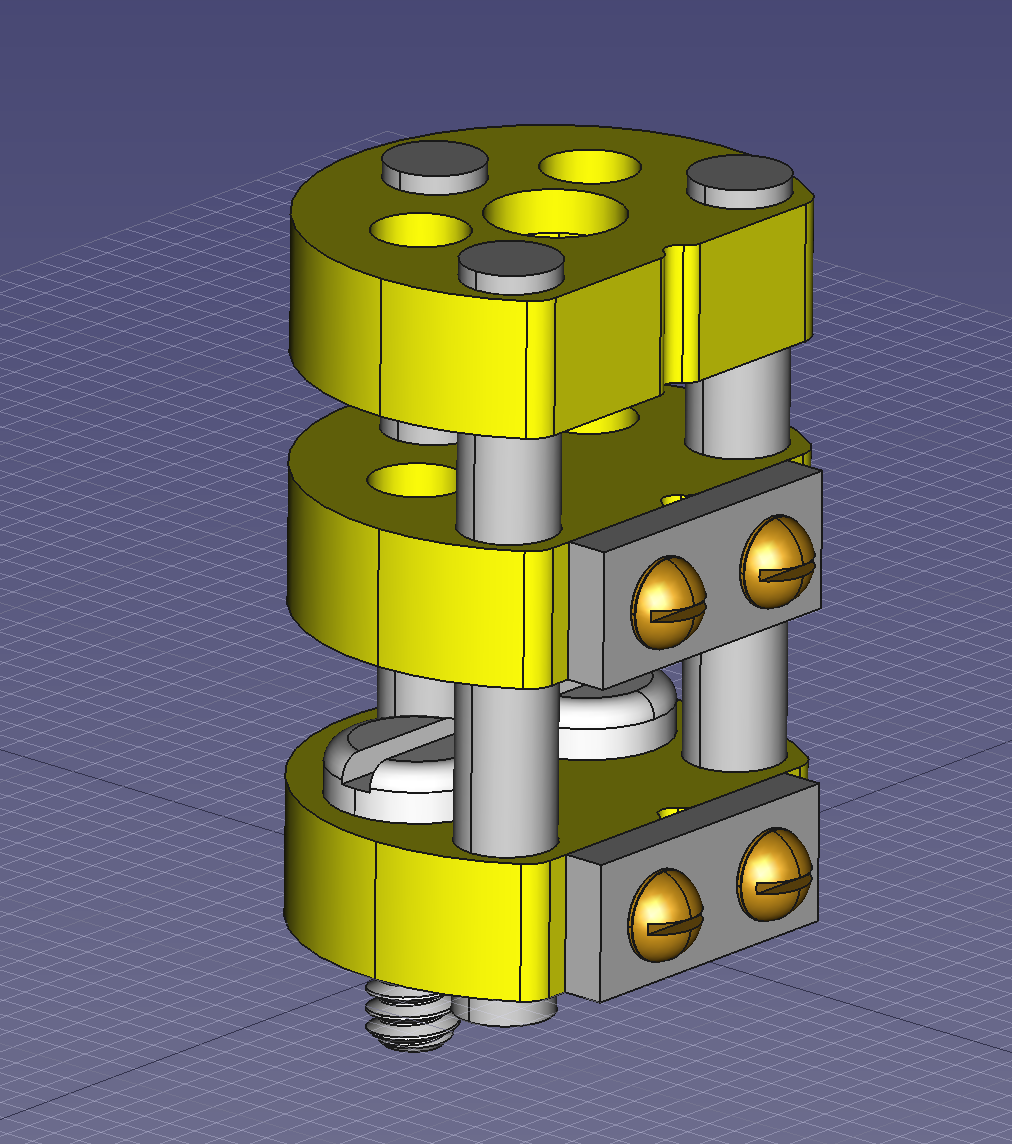
The additional screws used to assemble this cap are as follows:
Supplier | Part # | Description | Quantity | Cost |
---|---|---|---|---|
McMaster | 94609A848 | 10-32 Thread Size, 1/8" Long nylon round head slotted screw | 1 | $6.84 per 100 |
McMaster | 96295A705 | Low-Profile, M3 x 0.5 mm Thread, 3 mm Long Nylon Cheese Head Slotted Screws | 4 | $8.16 per 100 |
McMaster | 92991A106 | 4-40 Thread, 1/4" Long Brass Cup-Point Set Screws | 8 | $6.08 per 50 |
The .stl files for 3D-printing can be downloaded from Thingiverse. We have had good results printing prototypes of this design on the SCNI's FormLabs Form2 printer. For stronger materials that can be autoclaved prior to implantation, we've outsourced printing of the parts in carbon-PEEK (Impossible Objects) and Ultem 1010 (Stratasys). It should be noted that, despite earlier reports to the contrary (e.g. Mulliken et al.,(2015)), carbon-PEEK is now considered unsuitable for MR-compatibility due to it's conductivity.
This design extends the footprint of the original cylindrical chamber, but in doing so provides sufficient space to place a detachable connector block, which holds up to four 32 channel Omnetics connectors (for 2x 64 channel bundles, or 1x 128 channel bundle). Making the connector block detachable facilitates electrode replacements, while keeping the connector block independent of the microdrive cap makes replacement of broken caps easier.
Since the design is asymmetric, two versions are provided (denoted by suffix A or B on the .stl files), allowing the electrode to be located either anterior-lateral, anterior medial, posterior-lateral, or posterior-medial, depending on your needs. Either version of the connector casing and cap can be used in order to angle the connectors in such a way as to maintain easy access (e.g. avoiding headposts). The base (i.e bottom surface) of the chamber base can be further customized prior to printing by applying boolean subtraction of either a skull model, or some approximation of the skull surface.
The spacing between the Omnetics connectors has been selected to accommodate connection of a pair of Intan RHD2164 64-channel headstages. There re two options for installing the Omnetics connectros in the casing:
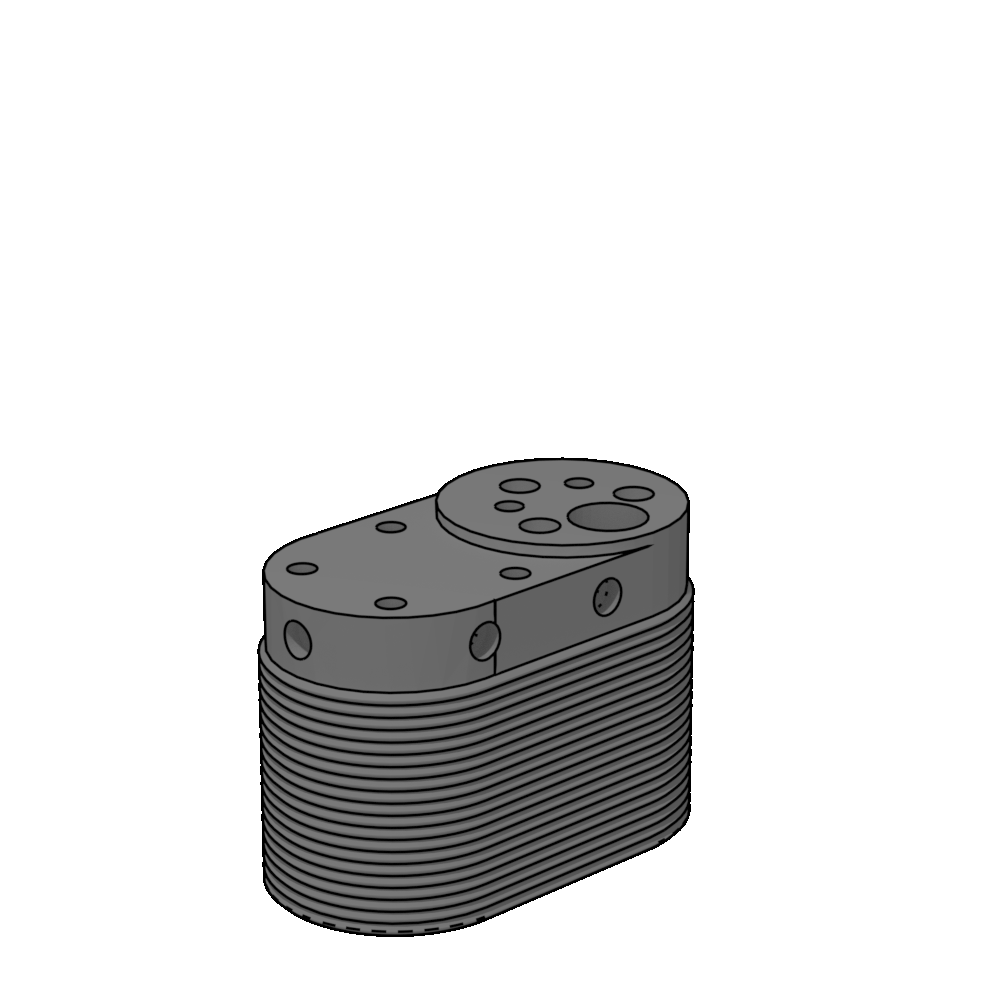
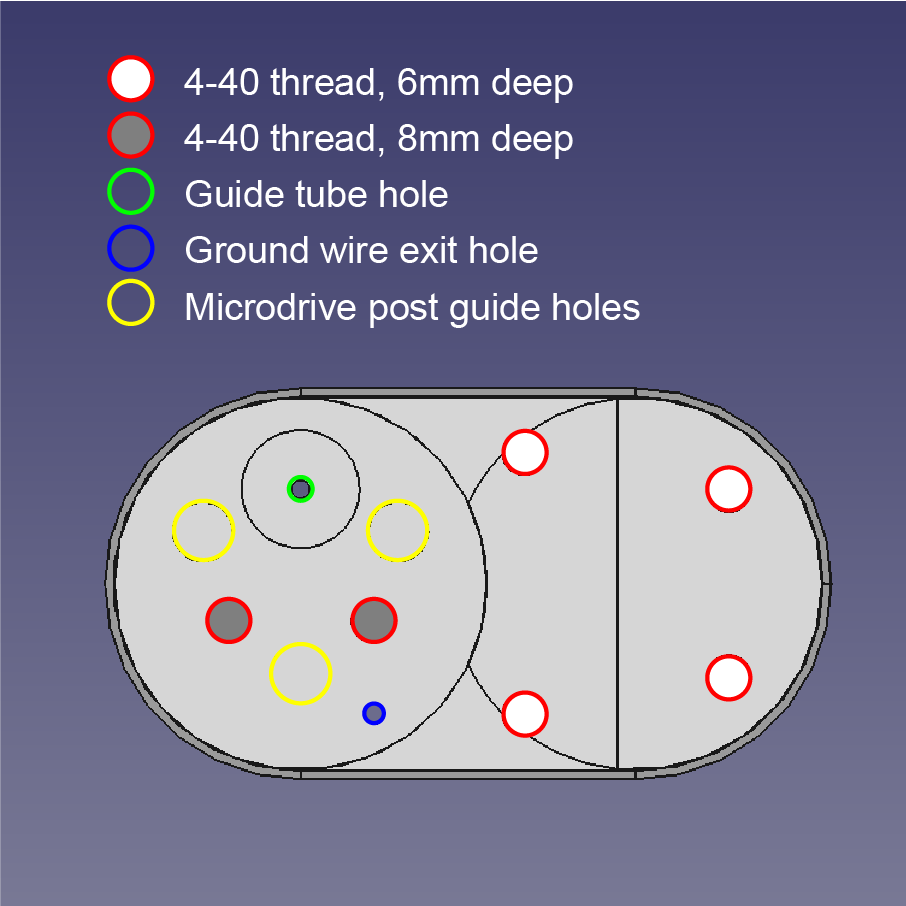
We outsource printing of these parts in Ultem 1010 - a high-strength heat-resistant plastic, which retains MR-compatibility whilst still allowing us to steam autoclave the parts prior to implantation. The current cost for a single implant (chamber base, connector case, and microdrive cap) from Stratasys is $338, although savings can be made for larger orders, and also by customizing the chamber base to better fit the skull prior to ordering.
The 3D printed parts should be sanded to ensure a smooth fit between surfaces in contact with each other. The small (1mm diameter) holes for the guide tube and ground wire may need to be drilled to ensure there is sufficient clearance (depending on the tolerances of the printing method). Additionally, six holes on the top surface of the chamber base should be tapped with a 4-40 closed-end tap (red circles on the above diagram), while the six holes in the sides of the cap should be tapped with a 4-40 through-hole tap.
The parts required for finishing and assembly of the connector casing are available from McMaster -Carr as follows:
Part Number | Description | Quantity | Cost |
---|---|---|---|
93939A714 | 4-40 thread, 1/4" nylon Narrow Fillister Head Slotted Screws | 8 per chamber | $5.99 for 100 |
92942A718 | 4-40 thread, 5/16" Nylon Pan Head Slotted Screws | 2 | $6.04 for 100 |
95862A533 | 1/4"-20, 11/32" Long Slotted Nylon Plastic Flat-Tip Set Screws | 1 | $7.80 per 100 |
27175A218 | 1/4"-20 Closed-End Hole Tap for plastic | 1 | $12.44 |
27175A112 | 4-40 Through-Hole Threading Tap for plastic | 1 | $13.49 |
27175A212 | 4-40 Closed-End Hole Threading Tap for plastic | 1 | $13.49 |
2546A23 | Tap Wrench handle | 1 | $17.88 |
4692A73 | 240-grit sand paper | 1 | $10.77 for 15 |
30565A211 | 1mm diameter drill bit | 1 | $1.79 |
The concept for the multidrive -an even smaller drive system than the original microdrive described in McMahon et al. (2014)- was inspired by the EDDS Array Drive. The need for targeting multiple sites in close proximity to each other in the same hemisphere lead to development of the multidrive. The drive screws are PEEK 4-40 thread machine heads, which pass through a 3D-printed thermoplastic drive shuttle. The wings of the shuttle keep it locked inside the drive shaft, while a channel on the front surface allows close mating with the electrode shaft, which is epoxied directly to it.
Part Number | Description | Quantity | Cost |
---|---|---|---|
94735A713 | Phillips, 2-56 Thread, 3/4" Long nylon pan head screws | One per drive | $5.70 per 100 |
27175A111 | 2-56 Thread, Through-Hole Threading Tap for plastic | 1 | $20.29 |