2.Gathering Pertinent Information - R-division-2020-2021-even/Repo-01 GitHub Wiki
What is a Moulding?
Molding or moulding is the process of manufacturing by shaping liquid or pliable raw material using a rigid frame called a mould or matrix. The liquid hardens or sets inside the mould, adopting its shape. A mould is a counterpart to a cast.
Types of moulding machine:
- Injection moulding machine
- Compression moulding machine
- Blow moulding machine
- Sand slinger moulding machine
INJECTION MOULDING MACHINE:
SI.No |
Electronics components |
Mechanical components |
Mechanism/working Principle Identified |
Links |
1. |
Heaters, Thermocouple, Split Mould/Cooling channels |
Ring plunger, Injection Unit, Clamp unit, Nozzle, Hydraulic system, Hopper |
The injection moulding process involves heating & injecting plastic material under pressure into a closed metal mould tool. The molten plastic cools & hardens into the shape inside the mould tool, which then opens to allow the mouldings to be ejected or removed for inspection, delivery or for secondary operations. It's working principle is similar to that of a syringe used for injection. It uses the thrust of the screw (or plunger) to inject the plasticized plastic in the molten state into the closed mould cavity. The reciprocating screw rotates by means of a motor and its reciprocating motion is provided by the hydraulic system. The Plastic granules are to be poured into the hopper and they will be pass through the chamber due to the rotation of the screw. The Heater heats the granules to its critical temperature. The thermoplastic molten liquid is pressurized (by the hydraulic system) outside the Assembly and allowed to travel through a nozzle of small diameter with high velocity and low pressure into the space between the moulds. The liquid will fill the mould with uniform compaction among the atoms and thereby density is uniform. After filling the liquid in the mould, by the cooling process, it will be solidified. Any shape and any size of the component can be produced with uniform density. Density can be controlled by varying the pressure in the pressure line and thereby production rate is high and wastage is recyclable. |
https://www.ssmachinery.com, https://learnmechanical.com |
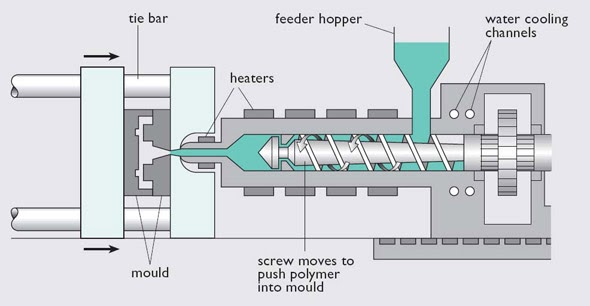
COMPRESSION MOULDING MACHINE:
SI.No |
Electronics components |
Mechanical components |
Mechanism/working Principle Identified |
Links |
2 |
1.AC Motor 2.Control panel 3.Heat sensor 4.Flow controle unit |
1.Extraction pin 2.Guide pins 3.Insulating plates 4.Hydrolic ram and cylinder |
In compression moulding processes, thermosetting materials are shaped between two halves of mould that constitute the cavity of the produced product.A piece of plastic material is placed on the bottom half of the mould, and the upper half is presses on this plastic material.The bottom half is generally preheated. And the piece of plastic material that is being placed inside the mould, is also heated with such systems.The piece of the initial charge of material can be in the form of pellets or semi-molten state. The heating of the initial plastic piece can be done with heated barrels which includes screw inside it, just like plastic injection moulding, infrared heater, or convection ovens. Pre-heating of charge shorten the process cycle time.Adjustment of required curing time for thermoplastic material is also a very important parameter. Curing of thermoset material takes place inside mold which is closed. Hydraulic systems are generally used to push or pull the two halves of mould in the compression moulding process. |
https://mechanicalenotes.com/compression-molding-process/ https://www.youtube.com/watch?v=sceetLZDyz0 |

BLOW MOULDING MACHINE:
SI.No |
Electronics components |
Mechanical components |
Mechanism/working Principle Identified |
Links |
3. |
Mould Clamping Device, Control Panel, Pneumatic System |
Extruder, Die Head, Cold Cutter, Sealing Equipment, Blow Pin |
Blow moulding is a moulding process used in the manufacturing industry to create hollow objects made of plastic. Like other moulding processes, it involves the use of heated, liquid material that’s forced into a mould cavity under pressure. Blow moulding is a special type of moulding process, however, that leverages the properties of traditional glassblowing.Blow moulding is a moulding process in which heated plastic is blown into a mould cavity to create a hollow object. The defining characteristic of a blow moulding is that it’s used to create hollow objects. Raw plastic is first heated, after which it’s formed into a parison. Next, the plastic parison is secured to the top of the mould. Finally, air blown down onto the plastic parison, thereby stretching it across the interior walls of the mould cavity.Blow moulding follows the same principle as glassblowing. With glassblowing, a glassblower blows air across heated glass, thereby creating a hollow glass object. With blow moulding, a machine blows air across heated plastic that’s placed on top of a mould cavity. The air forces the heated plastic to expand across the interior walls of the mould cavity |
https://www.yankangmachine.com/extrusion-blow-molding-machine-parts-name/ |
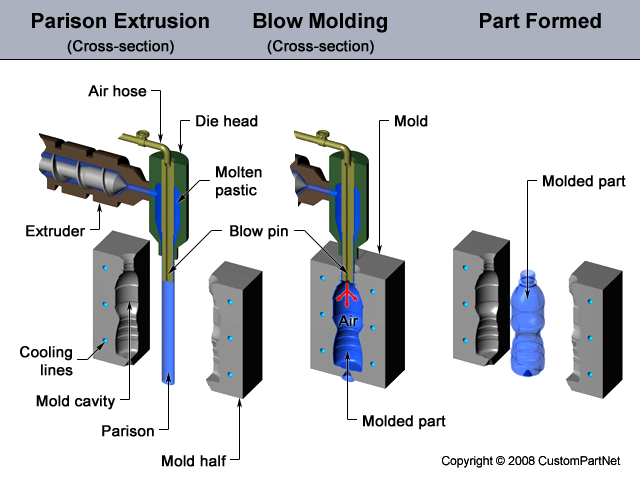

SAND SLINGER MOULDING MACHINE:
SI.No |
Electronics components |
Mechanical components |
Mechanism/working Principle Identified |
Links |
1 |
DC motor connecting shaft,spur gear,lead screw |
Belt conveyor,hopper,sand impeller, movable or swinging Arm |
A stationary sand slinger is a type of machine used for filling and uniform ramming of sand in casting molds, and is particularly adopted with advantage of large molds. ... Sand slinger fill the flask uniformly with sand under high pressure stream throwing the sand with high speed by impeller.The speed of the ramming unit motor also influences mold hardness and the Sand Slinger is provided with a dual speed ramming unit motor to provide operator selection of two ramming hardnesses.A stationary sand slinger is a type of machine used for filling and uniform ramming of sand in casting molds, and is particularly adopted with advantage of large molds. |
http://www.simpsongroup.com |
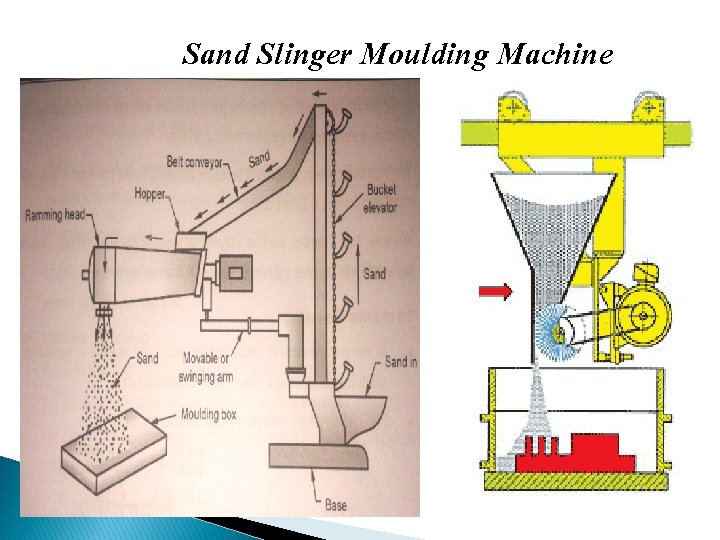